Petrovax’s biotechnological manufacturing and warehouse complex was opened in the Moscow region in 2008.
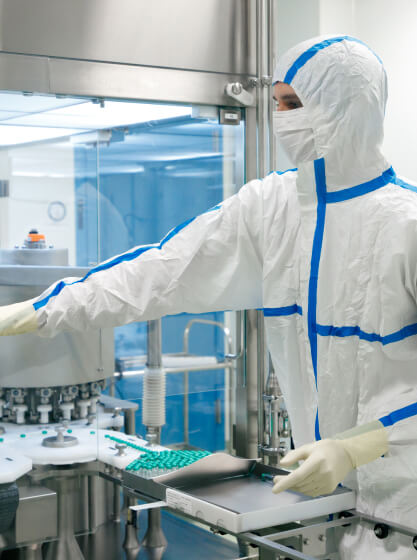
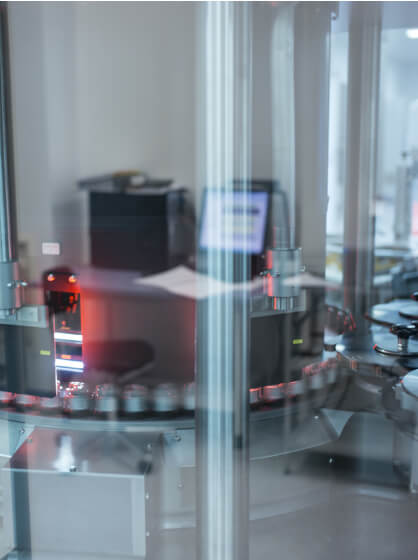
manufacturing facilities include 4 production lines
The manufacturing processes include the synthesis of APIs, the production of sterile and non-sterile medicines, including immunological and biopharmaceutical drugs in various dosage forms. Manufacturing capacity is more than 160 million doses of products per year. The company owns a pharmaceutical warehouse that provides appropriate storage conditions for medicinal products.
-
Line 1
the release of medicines in pre-filled syringes
-
Line 2
manufacturing of medicines for injection, including lyophilisates
-
Line 3
synthesis of substances, manufacturing of soft and solid dosage forms
-
Line 4
manufacturing of injectable dosage form
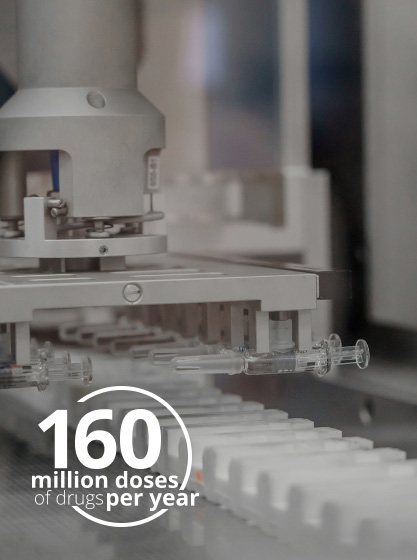
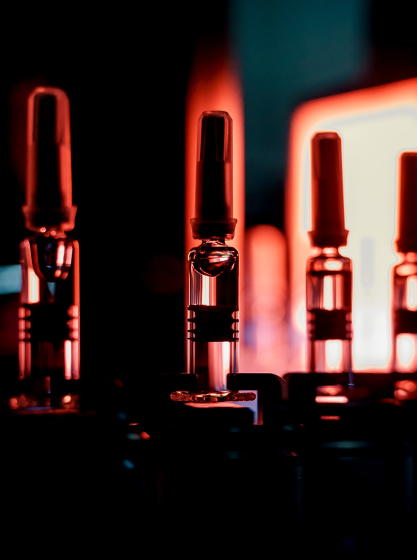
-
Line 1
the release of medicines in pre-filled syringes
-
Line 2
manufacturing of medicines for injection, including lyophilisates
-
Line 3
synthesis of substances, manufacturing of soft and solid dosage forms
-
Line 4
manufacturing of injectable dosage form
Every year the company successfully confirms compliance of production with international standards during audits of regulatory authorities for licensing and GMP certification, as well as inspections of international partners: Pfizer, Abbott, Boehringer Ingelheim.
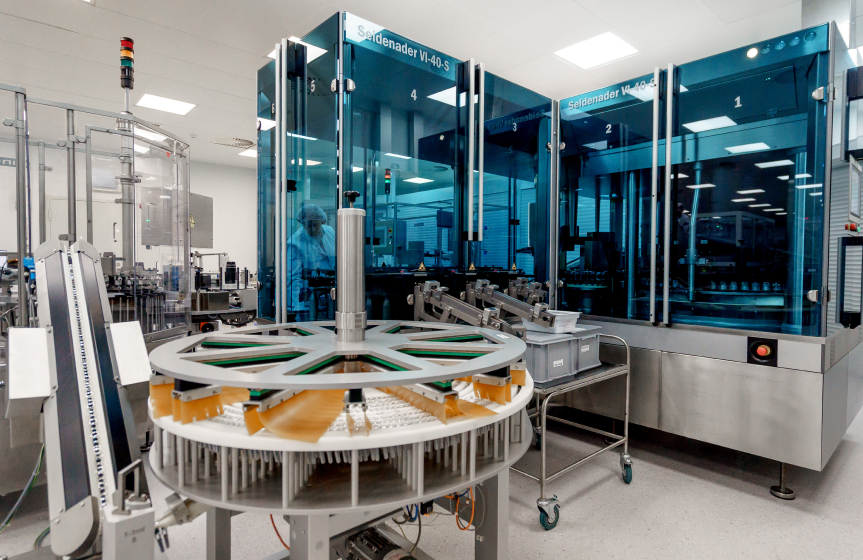
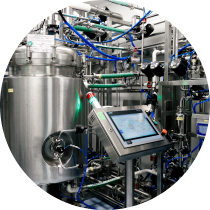
Automated substance synthesis system
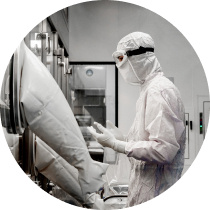
Vaccine filling control
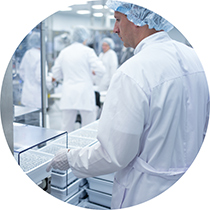
Loading of pre-filled syringes onto the inspection, packaging and labeling line
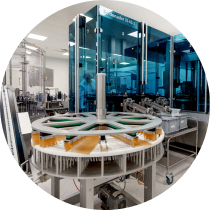
Automatic inspection machine for pre-filled syringes
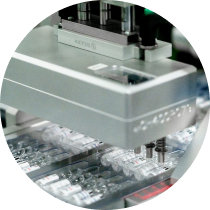
Pre-filled syringe inspection, packaging and labeling line
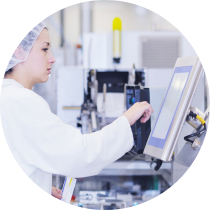
Automatic serialization and aggregation line of medicines, packaging section of pre-filled syringes
manufacturing complex
1 Sosnovaya St., Pokrov village , Podolsk, Moscow region, Russian Federation 142143
Ph.: +7 495 926-21-07
Email: npo@petrovax.ru
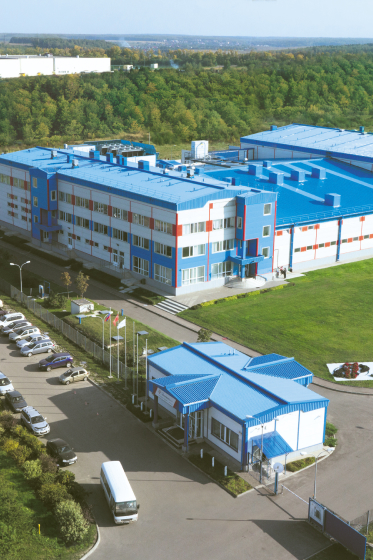
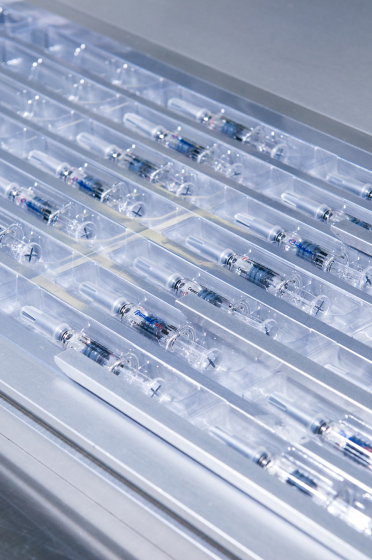